作為二板智能注塑機專家,博創智能裝備股份有限公司(以下簡稱“博創”)在大型二板智能注塑機的研發與制造方面,無論是單色,還是多組分機型,整體技術水平在國內同行業中處于領先地位。
長久以來,博創始終致力于促進產業進步,倡導設備向大機二板化、小機電動化、整廠智能化方向發展。“我們緊密圍繞這三個核心議題開展研發活動,以先進智能技術裝備為標桿,專注于工廠的數字化組織生產和營銷,尤其注重發掘那些需求明確,且能夠與我們產品實現良好對接的客戶。”博創董事長朱康建說。
如今,技術創新已成為推動高質量發展的核心動力。在此背景下,博創實施了“創新驅動發展”戰略,積極與國內各大高校開展產學研合作,承擔和參與了國家智能制造新模式應用項目、國家數控一代機械產品等項目,多個產品被列入國家首臺/套重大技術裝備,多年榮獲國家智能制造重大榮譽和專項。今年,博創二板智能注塑機榮獲廣東省單項冠軍,進一步證實了企業定位和科技創新所取得的豐碩成果。
早在2010年,朱康建就前瞻性地提出“數字博創”口號,公司全面實行精益生產、數字化管理,還設立專項資金投入智能制造。而直到2015年,“工業4.0、智能制造”等話題才在國內興起。如今,在智能制造轉型升級的關鍵時期,他依然堅定和冷靜,他的想法和判斷也成為行業重要的參考。
“我認為,機遇與挑戰并存,未來是留給有準備的人。”
“談智能制造,毫不夸張地說,我們是整個塑料機械圈子中第一個提出來的。”
朱康建是自信的。
早在2015年,博創成功入選國家首批46家智能制造試點示范企業之一;2021年,又成為國家智能制造示范工廠揭榜單位,這也是迄今為止,塑料加工設備制造企業榮獲的唯一一個國家級智能制造實體示范榮譽。
朱康建又很謙虛。“其實我們也做得不夠好,只是做了一個先行者的角色。過去的10年,可以坦率地說我們落后了,在硬件投資方面偏弱,這導致整體規模化的生產能力與主要競爭對手相比稍微有所落后。我們必須首先正視這個問題,才能找到進步的空間。”
朱康建也是果斷的。他找準了兩個發力點,第一,搭建平臺化、系統化的智能制造產品,為此特別成立了廣州中和互聯網技術有限公司,將每臺設備連成線,再將線織成網,幫助客戶實現數字化、智能化生產的部署;第二,博創內部進行智能化升級,通過與全球優秀的軟硬件供應商合作,加快向數字化工廠邁進的腳步。
果斷是在關鍵時刻準確把握機會的決策能力。自此,博創也開始了一場與各領域頭部企業合作的大幕。
與美的集團合作開始于15年前。“我們從數字化、自動化、先進工藝等多個方面進行研究和突破,提升注塑工廠的數字化和智能化管理水平,減少生產過程中的高能耗環節,達到注塑生產中零故障率,顯著降低生產成本、提高生產效率。”朱康建介紹,如今,博創正為美的荊州工廠提供協助,該工廠擁有超過一百臺中大型注塑機,基本實現24小時黑燈作業。
“想要與行業No.1合作,你也要成為這樣的企業,具備一流的技術實力和產品品質,以實現相匹配的協作水平。博創足夠優秀,才能夠跟美的、TCL這樣是頂尖的家電巨頭,以及比亞迪新能源汽車頭部企業開展合作。這說明了我們長期以來的研發投入、創新實踐和文化建設,已獲得了廣泛的肯定與認同。”朱康建表示。
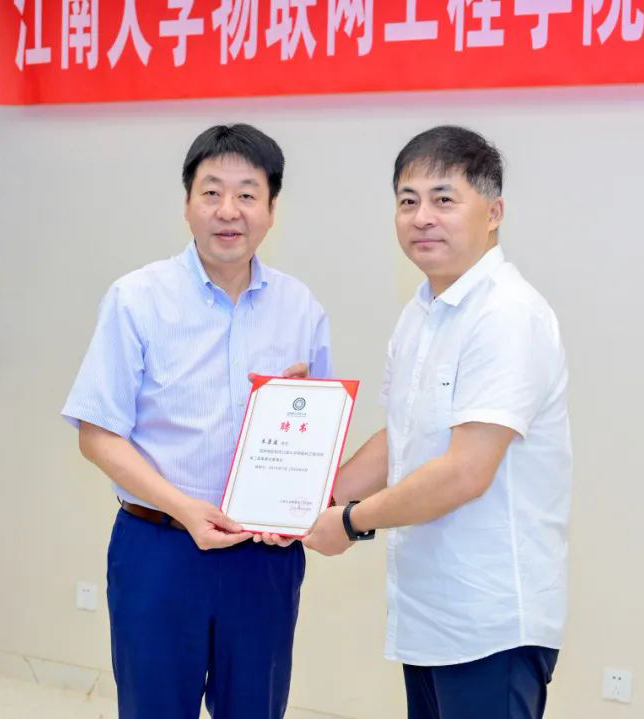
朱董連任江南大學物聯網工程學院董事會董事長
幾乎從成立的第一天起,博創就處在產業智能改造的最前沿:在注塑機人機交互界面(電腦)上即可對周邊輔機進行智能互聯,實現閉環控制;為注塑企業提供完善的生產管理平臺,解決工廠設備管理痛點問題;實現對設備狀態的實時監控、智能預警,提高異常響應速度,提升設備利用率。
博創正在充分發揮自身在智能制造領域的優勢,為客戶提供優質的解決方案,助力企業實現數智化轉型。
“每個人都在講科技創新,只是重復說這四個字沒有任何的意義。”
朱康建認為,科技創新最后一定體現在服務客戶的能力方面。
就在《塑膠工業》采訪當天,博創3300噸大型三色對射注塑機正式交付比亞迪。這是國內領先的大噸位多物料注塑裝備,融合了大型二板機、獨立射臺、水平轉盤、疊模以及伺服驅動控制等多項先進技術,充分展現了博創在二板機、多組分技術以及轉盤技術控制方面的深厚理解和專業能力。
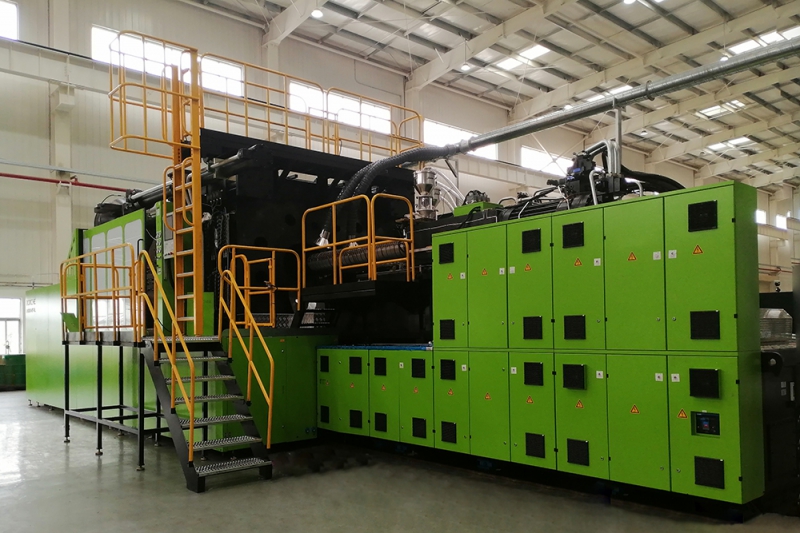
BM3300-MT-ML博創大型三色對射注塑機
“我們與比亞迪攜手應對了一項前所未有的挑戰。3300噸級的大型對射注塑機從接受任務到交付成品,我們僅用了不到100天。這創造了多項全球首次。”朱康建介紹,過去,車燈生產需要組裝十幾個零件,而博創通過技術創新,成功將其簡化為單個的整體部件,注塑精度要求極高。“在先前的交付過程中,該機型一次性通過驗收,并隨即投入運行。”
去年,博創開始與新能源汽車領導者比亞迪合作。目前已有大批博創注塑機入駐比亞迪工廠,服務于比亞迪汽車內外飾件、大燈面罩、裝飾框等汽車零部件的生產。
為了提升產能,縮短交付時間,博創工廠從各個環節尋找提升效率的空間。自2020年起,先后增加了多條自動化生產線,實現從部件到總裝的自動化,為提升產能和交付能力做好準備。與此同時,隨著自動化改造和生產現場改善,博創搭建了精益管理平臺,加快智能制造生態體系建設。
“其實,交付能力最能體現企業的整體制造水平。講個現實案例,昨天我們還在選購加工中心,日本、歐洲品牌交付期起步都是一年。相比之下,博創僅2500噸對射設備每月可以提供4臺,從零部件生產,到機架出廠,我們最快只需要10~14天,一臺機器可以出貨了,同樣是結構復雜的大型設備。”朱康建說。
如今,博創所展現的技術創新成熟度,以及制造能力和協作能力,連同員工技能的提升,均達到了非常高的水平。“與加工中心的當前狀況一樣,在注塑機產業中,我們同樣擁有卓越的產品品質,并展現出顯著的交付能力,完全具備了進軍全球高端市場領域的實力。”朱康建表示。
“近期,我們承接了一項來自紐約客戶的訂單,要求在65天內交付首臺2200噸的設備。該設備需按照美國標準進行生產,由于客戶的廠房設施較為陳舊,需要配備抽拉桿。在不到兩個月的時間內,我們已成功地將設備從中國碼頭發出。”朱康建說。
博創要做一家偉大的企業,就要有能力解決從0到1的過程。
“如果不抓好國內市場,企業活不下去;如果不開拓國外市場,企業得不到持續的發展。”
自2017年在英國設立分公司以來,博創持續實施國際化戰略,包括建立海外倉庫,聘請當地銷售與服務團隊,如今已在全球范圍內成立了五家全資或合資控股公司。這一系列舉措不僅滿足了企業自身發展的需求,也順應了全球化趨勢,從而把握住國際擴張的結構性優勢。
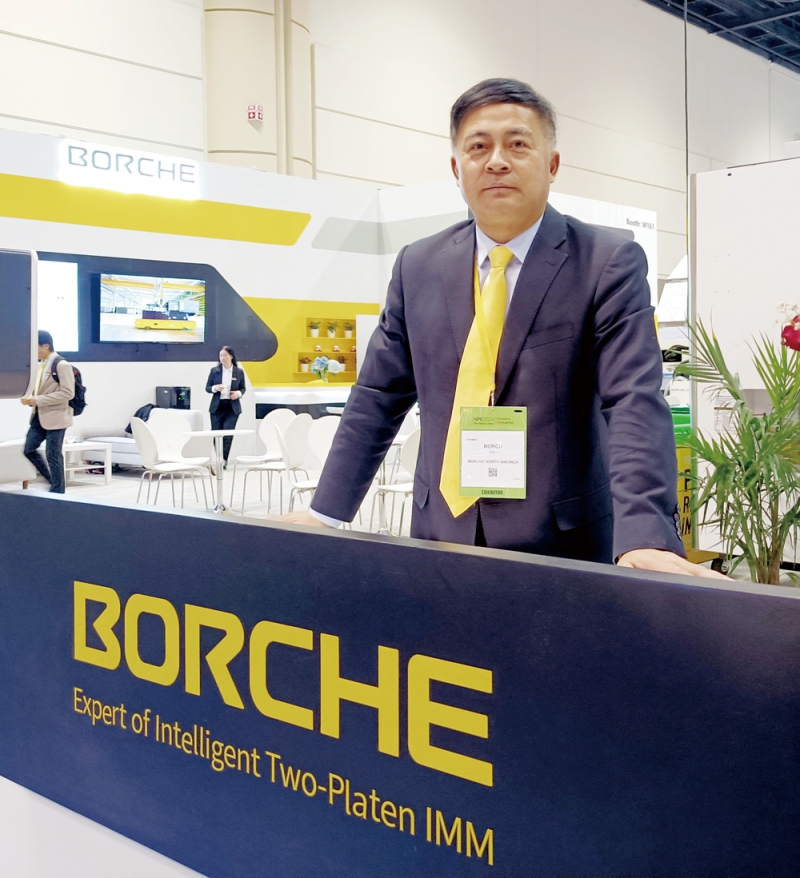
朱康建參加了美國NPE展會
海外業務的快速增長,正成為企業壯大的重要力量。統計顯示,博創超40%的營業收入來自于海外,以歐洲、北美地區市場為主,合作代理覆蓋全球60+國家/地區。
“國際化既是風口,充滿機遇,也是考驗。我們必將依據當地客戶的需求、市場偏好以及競爭格局,與當地銷售策略相協調,進行設備的研發和相關推廣服務。我們不會簡單地將產品直接銷售,因為這種做法并不適宜。”朱康建表示,博創針對不同地區、不同國家,從機器配置、性能到顏色等方面,均致力于實現產品的本地化。“我認為,我們因為努力收獲了成功。”
對于國際市場,他一直抱有很高的期望。
今年5月份,朱康建參加了美國NPE展覽會,并與美國客戶進行深入的交流,積極聽取他們的反饋意見。“實際上,對于中國注塑機品牌而言,全球接受度正在逐步提升。我們在現場接到了多臺大型設備的訂單,這不僅僅體現在數量上,更是對我們的交付能力、機器性能、服務質量以及性價比方面的充分肯定。”
如今,國產設備通過不斷在市場中競爭,已經積累了一定的資歷,展現出強大的競爭力。“當然,在電動化領域與日本相比,在大型化領域與德國、奧地利、意大利等國家相比,仍存在一定的差距。這些差距恰恰指出了我們的發展空間。我們充滿信心和決心,并且承擔著責任,要在全球舞臺上展現中國塑料機械行業的風采。”朱康建說。
而在未來,博創將持續加強“全球博創”戰略,深耕海外市場,致力于將“高端科技,中國制造”推向全世界。
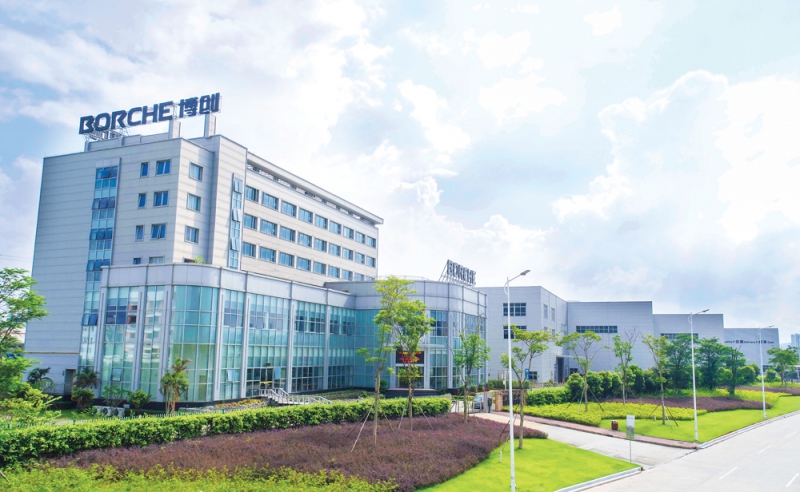
博創智能工廠與康建創新中心
你的員工心齊嗎?
你的團隊足夠優秀嗎?
你的創新實現可持續了嗎?
你的智能化水平提高了嗎?
你的單位制造成本做到行業最佳了嗎?
再回看這些提問,朱康建強調,博創堅守一個核心理念,就是修煉內功。
他表示,博創的發展狀況,實則取決于內部的準備工作是否充分,特別是體系化和數字化建設的成效。
值得肯定的是,在研發領域,博創每年投入巨額資金,總計四五千萬元的研發經費,包括人才培養和品牌建設方面的投入,這些確保了企業業績每年兩位數的增長。而資源整合是博創內部進行資金與技術深度挖掘的關鍵。
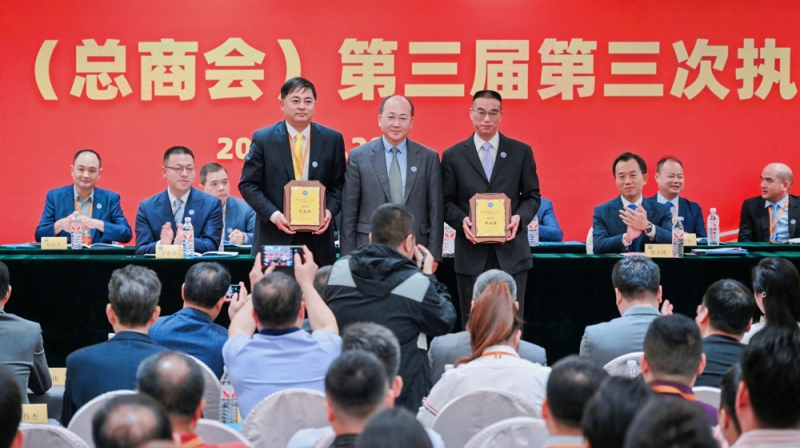
朱董當選增城區工商聯副主席
在體系化建設方面,博創圍繞設備模塊化設計、零件加工精度的提升,以及更具針對性的技術研發,構建了多元化的產品和服務體系。例如,針對托盤專用機械的專項研究,已使博創在該領域內處于領先地位;在車燈注塑機領域取得的顯著成就,幾乎達到了國內領先水平。
朱康建透露,關于電動化高速薄片技術的討論,是博創正在進行的項目。“長期以來,包裝行業超薄片領域一直被德國的幾個知名品牌壟斷。我們相信,通過推動電動化和高速化技術,我們有機會打破這種局面,開辟中國塑企進入高端裝備市場的先河。”

朱康建攜全體高管攀登廬山
“而在數字化方面,未來3到5年內,我們還將投入幾個億的資金,加速智能化與數字化轉型進程。我認為企業規模不一定要做到最大,但運營效率及單項經濟指標定將躋身行業翹楚之列。”小而美、美而精的想法,是朱康建從企業生態圈的角度去理解了企業定位。
今年,國家對經濟工作給予高度重視,提出加快培育新質生產力,助力中國經濟增長和民族復興。特別重視提升高端智能化裝備,促進制造業轉型升級,一系列力度大、范圍廣、影響深遠的政策密集出臺。
對高端裝備制造企業來說,這是積極信號。如今,博創已經是國家專精特新“小巨人”企業,但朱康建覺得還是不夠。“我們的目標不僅僅是成為國內細分市場的佼佼者,而是要力爭在國際舞臺上占據一席之地,成為該細分行業的全球領先者。”