摘要:針對常規的管材液壓成形技術需要昂貴的專用設備及模具、生產效率低等不足,開發了一種簡單實用、可在沖床或壓力機上使用的管材沖擊液壓成形裝置,可用于薄壁金屬管材的自然脹形、軸壓脹形和異形截面中空件的沖擊液壓成形。該裝置無需外部高壓供給系統和專用液壓成形設備,通過撞擊軸壓頭擠壓容腔中液體的方式來為管材提供液壓力和軸壓力。通過設計軸壓頭的行程和調節溢流閥的溢流壓力值等來實現最大液壓力和軸向進給量的合理匹配,并以304不銹鋼毛細管和H65黃銅毛細管為試驗管材做了相關試驗。研究結果表明:該裝置結構簡單、操作方便;可實現最大液壓力與軸向進給量的協調控制;合理的載荷匹配能顯著地提高管材沖擊液壓成形的成形性能;H65黃銅毛細管破裂時所需的液壓力小于304不銹鋼毛細管破裂時所需的液壓力。
關鍵詞:管材;沖擊液壓成形;最大液壓力;軸向進給量;載荷匹配
沖擊液壓成形技術(Liquid Impact Forming,LIF)是在管材液壓成形技術(Tube Hydro- Forming,THF)的基礎上進行改進的。THF是用于生產截面形狀復雜的薄壁管狀零件的一種先進、特殊、精密(半精密)的凈成形技術,具有成本低、工序少、質量輕、剛度高等特點,但是常規的THF技術需要昂貴的專用設備及模具,而且生產效率低(只有傳昂貴的專用設備及模具,而且生產效率低(只有傳統沖壓方法的1/3)[1-3]。針對THF技術的不足,美國Greenville Tool&Die公司最近提出一種新型成形技術—LIF技術。LIF技術是一種通過結合沖擊和液壓成形,將薄壁管或薄壁板成形為不同形狀零件的成形技術,其原理是液體介質受到高速運動的沖擊體擠壓,瞬時變為高壓液體而作用于零件表面,進而獲得期望的脹形件。該技術因具有成形速度快、成形質量高、成本低等特點而被應用于汽車、航空工業領域[4]。
在LIF中,動能、電能、化學能等可為沖擊的動力源,因其能量利用率高而在其他文獻中稱之為高能率沖擊液壓成形。目前,關于沖擊液壓成形的研究較少,鮮見相關文獻。在國外,白俄羅斯Chachin V N等[5]用壓縮空氣為動力源的設備研究了沖擊液壓成形技術。南非的Kosing O E等[6]開展了沖擊液壓成形的工藝參數理論和實驗研究。這些國外學者所使用的設備或裝置都是以壓縮氣體作為動力源。在國內,中國科學院金屬研究所徐勇等[7]研究員已開始研究相關高能率沖擊液壓成形技術。桂林電子科技大學Huang C M等[8]開展了相關沖擊液壓成形裝置的研究,其裝置是以電能為動力源。目前,該技術雖然在工業上已得到應用,但尚未得到推廣。管材LIF技術是一項極具發展潛力的先進成形技術,因此,開發一種管材LIF裝置可挖掘管材LIF技術的研究和應用價值。
針對現有的LIF裝置存在結構復雜、操作不便等不足,本文開發了一種新型的管材LIF裝置,該裝置不僅不需復雜的外部液壓供給系統,而且無需螺釘等連接零件,更便于試驗操作。
1.管材沖擊液壓成形裝置的設計
1. 1結構設計特點及要求
本文開發的管材沖擊液壓成形裝置示意圖如圖1a所示,其主要結構特點及要求如下。
(1)高壓液體的生成。在管材沖擊液壓成形中,在管材內腔形成高壓液體是管材成形的必要條件。如圖1所示,安裝有Y型密封圈的軸壓頭在外載荷S的作用下,高速擠壓容腔內的液體,使其內部液壓力急劇升高,高壓液體同時通過軸壓頭的通液孔進入兩段密封的管材內腔,進而使管材得到成形所需的液壓力。為保證管材能達到預期的變形程度,容腔內的液體體積的變化應大于管材塑性變形后內腔容積的變化,當管材內部的液壓力達到預定的溢流壓力值時,溢流閥開始溢流。
圖 1管材沖擊液壓成形裝置的示意圖 ( a)和實物圖( b)
1. 軸壓頭 2. Y 型密封圈 3.容腔 4. 管材 5. 模腔 6. 密封柱 7. 定位圈 8. O 型密封圈 9. 液體
(2)實驗裝置的密封。實驗裝置的良好密封性是決定管材達到預期成形效果的一個重要因素,因此,在管材兩端必須要有良好的密封。在本成形裝置中,管材兩端的密封原理一樣,區別在于O型密封圈的密封點不同。安裝于容腔中的O型密封圈對管材上端外壁進行密封,而安裝于密封柱中的O型密封圈對管材下端內壁進行密封,當軸壓頭擠入裝滿液體的容腔中后,由管材兩端的O型密封圈對管材內部形成了初始密封。軸壓頭受到撞擊而推動管材下移,管材兩端部分別被擠到軸壓頭、密封柱中的錐形臺階上,與O型密封圈共同作用,實現了管材兩端的再次密封。
(3)軸向進給量的控制。管材在成形過程中,為防止管材出現屈曲、彎曲等成形缺陷,成形區需要得到有效地補料,而在沖擊液壓成形中,軸向進給量是補料量的決定因素。軸壓頭的軸肩頂在管端,推動管材下移,軸壓頭下移量與管材的軸向進給量成正比。本裝置先通過在裝置下面放置墊塊初步調整裝置距沖頭的距離,再通過微型沖床的行程調整螺進行微調,從而準確地控制管端軸向進給量。
(4) 最大液壓力與軸向進給量的協調控制。在LIF過程中,合理的加載路徑可以有效地挖掘潛在的管材成形性能,本裝置可以通過墊塊等控制軸向進給量,但由于成形過程所需要的時間極短而導致液壓力難以控制,而安裝在溢流口處的溢流閥可以有效地控制管材脹形過程中的最大液壓力。本裝置通過調節行程調整螺和設置溢流閥中的溢流壓力值,來實現最大液壓力與軸向進給量的協調控制。
1.2 主要參數的確定
本裝置的主要參數是設置在容腔中的液壓腔尺寸及設置在軸壓頭中的通孔直徑大小,可根據下述方法來確定。
1.2.1液壓腔的尺寸
液壓腔的尺寸設計是基于文獻[9]中所述的方法來確定。
(1)液壓腔直徑。根據文獻[9]所述,液壓腔體積V的減小應大于管材塑性變形后管材內腔體積的變化量V變與液壓腔中所密封的空氣之和。本裝置中,在軸壓頭擠入液壓腔的過程中,將容腔中的空氣排盡。因此,液壓腔體積V只要滿足式(1)即可。

液壓腔為圓柱體,其體積為:

式中:h為軸壓頭在液壓腔工作時滑動的高度,mm;dc為液壓腔直徑,mm;d1為軸壓頭處在液壓腔液體中的軸直徑,mm,其值取試驗管材外徑D0。
管材塑性變形后管材內腔體積的變化量為:

式中:K1為修正系數,取1~2;R0為管材內半徑,mm,R0=d0/2;d0為管材內徑,mm;R2為管材脹形區兩端部的圓角半徑,mm,R2=R1-R0;R1為管材最大脹形半徑,mm;l1為管材脹形區長度,mm。
為提高裝置的穩定性,可降低裝置重心,則h=dc,將式(2)、式(3)代入式(1)中即可得到液壓腔直徑:
(2)液壓腔深度。軸壓頭與容腔中的液壓腔為滑動配合,軸壓頭需對容腔導正,則液壓腔深度為:

式中:l2為容腔中液壓腔的導正長度,mm,根據經驗,取l2=h/4。
1.2.2 軸壓頭中通孔直徑
在管材成形過程中,液壓腔中的液體應能有效地補給到管材脹形區內,否者管材因得不到充分的脹形而影響成形質量。在管材沖擊液壓成形中,在軸壓頭受到撞擊時到管材脹形成形結束這段時間t內,軸壓頭中通孔允許液壓腔中液體進入管材內腔的最大的體積量V進應大于管材塑性變形后管材內腔體積的變化量,即:

液壓腔中液體通過軸壓頭中通孔進入管材,其進入液體體積為:

式中:d2為軸壓頭中通孔直徑,mm;v為軸壓頭擠壓液體的速度,(mm•s-1)。將式(3)、式(7)代入式(6),可得:

1.3 裝置主要工作方式
(1)自然脹形。將軸壓頭設計為凸型塊(即不需要軸壓頭中通孔部分,使得軸壓頭與管材無接觸)并安裝Y型密封圈,將其擠入容腔中,軸壓頭下行,高壓液體通過軸壓頭中的通液孔進入管材內腔中,管材脹形區因受急劇增大的液壓力開始自然脹形。
(2)軸壓脹形。將軸壓頭設計為圖1a中所示階梯軸式,將其擠入容腔中,軸壓頭受到撞擊,高壓液體通過軸壓頭中的通液孔進入管材內腔中,管材在軸壓頭施加的軸向力和高壓液體的液壓力共同作用下,進行軸壓脹形。
(3)軸向進給量、最大液壓力對成形極限的影響規律。調節行程調整螺設置不同軸向進給量,通過設置溢流閥的溢流壓力值(即最大液壓力),則可研究最大液壓力與軸向進給量的協調控制下對管材成形極限的影響規律。
(4)成形異形截面中空件。將成形模腔安裝在如圖1a所示裝置的容腔和定位圈,采用(1)或(2)工作方式即可成形出各種異形截面中空件。
2.試驗驗證
2.1試驗條件
將管材沖擊液壓成形技術應用于微型管成形中,將會獲得更加高效、省時的生產方法[10-11]。本試驗管材為304不銹鋼毛細管和H65黃銅毛細管,其幾何參數如表1所示。取修正系數K1=2,將表1中相應參數代入式(4),得dc>5.57mm。由于所選的Y型密封圈外徑為Φ17mm,依據所安裝Y型密封圈的槽形圈尺寸標準要求,取dc=16mm,代入式(5),得h'=20mm,結合容腔通孔直徑為Φ6mm、Y型密封圈高度為5.8mm,則容腔內液壓腔的實際深度為29mm。本試驗在TUB-5T微型沖床上進行,其沖頭的平均速度為軸壓頭擠壓液體的速度,為20mm•s-1,代入式(8)得d2為2mm(為加工方便,取整數)。墊塊高度及溢流閥設置為:(1)墊塊高度不變,取溢流壓力值為最小值、中間值、最大值,其試驗組編號分別為1、2、3;(2)將溢流壓力值設置為最大,在前面的試驗基礎上,根據試驗經驗添加一塊厚度為2mm的墊塊,其試驗組編號為4。
表1 4管材幾何參數
2.2 試驗裝置
試驗裝置裝配好后的實物圖如圖1b所示。軸壓頭上端部設有法蘭,與容腔上表面相距12mm,以便有足夠的距離使軸壓頭下降以及安裝和卸載。成形模腔外形為T形狀,便于其安裝及容腔和定位圈的定位,成形模腔接觸容腔底面的表面起到支撐容腔和定位O型密封圈的作用,成形模腔開設有喇叭口且不限制管材脹形區的變形(即自由脹形),便于觀察管材變形過程,其高度(即管材的脹形區長度)為10mm。壓力表和溢流閥組件通過接頭與容腔連接,壓力表和溢流閥的工作壓力范圍分別為0~100MPa和60~100MPa。由于受到微型沖床的高速撞擊,裝置中的液壓力會產生波動,若用一般的壓力表,則會導致指針不能歸零,故為得獲得基準的液壓力值選用抗震壓力表。
2.3 試驗過程
試驗時,將管材置入由容腔、成形模腔和定位圈所形成的型腔中,向容腔中注滿液體,將軸壓頭置入容腔的環形凹槽中,調定好溢流閥溢流壓力值后,將試驗系統放置在微型沖床上。啟動微型沖床,沖頭以25mm•s-1左右的速度撞擊軸壓頭,管材內部的液壓力急劇增大,沖頭推動軸壓頭下移所設定的軸向進給量后,軸壓脹形結束。卸載裝置,取出管材,試驗結束。
2. 4試驗結果
圖2為采用該裝置進行相關試驗得到的試件實物圖。表2、表3分別為4個試驗組所獲得304不銹鋼毛細管和H65黃銅毛細管的試驗結果,表2和表3中的“/”表示因屈曲而不可獲得最大脹形高度。從圖2可知:在同一進給量下,3種不同的溢流壓力值中,304不銹鋼毛細管的脹形效果不一樣,溢流壓力值為中間值時效果最好,最小值時并未脹形,最大值時管材破裂; 在溢流壓力值設置為最大、墊塊高度合適時,試樣管材都發生了破裂,而且其脹形輪廓是一條光滑曲線,而墊塊高度過高時,試驗管材不僅脹破還發生了屈曲,該原因是由于軸向進給量過大,在液壓力共同作用下導致試驗管材屈曲嚴重。而對于H65黃銅毛細管,在溢流壓力為最小值時,就已破裂,由此可知,H65黃銅毛細管的塑性比304不銹鋼毛細管差。
圖 2.脹形后相應試驗編號所得到的管材實物圖
( a) 試驗組 1 ( b) 試驗組 2 ( c) 試驗組 3 ( d)試驗組 4

表2 各試驗組所得304不銹鋼毛細管的試驗結果
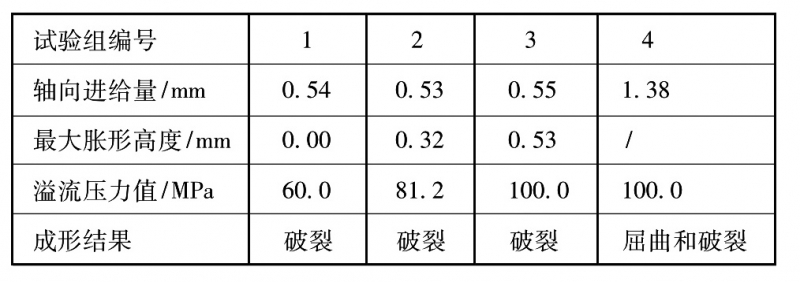
表3 各試驗組所得H65黃銅毛細管的試驗結果
3.結論
(1)開發了一種新型的管材沖擊液壓成形裝置,在普通的沖床、壓力機上即可實現最大液壓力與軸向進給量協調控制,并進行管材沖擊液壓成形試驗,獲得管材的成形性能參數。
(2)試驗結果表明,該裝置在微型沖床上進行管材軸壓脹形,順利地完成了高壓液體的生成、管端的高壓密封、軸向進給量的控制和最大液壓力與軸向進給量的協調控制,工作穩定可靠。
(3)試驗分析表明,最大液壓力和軸向進給量可以有效地提高管材的成形性能,防止管材屈曲、破裂等成形缺陷;在H65黃銅毛細管和304不銹鋼毛細管為試驗管材時,H65黃銅毛細管破裂時所需的液壓力小,使用溢流閥時,易獲取脹形成功的304不銹鋼毛細管。